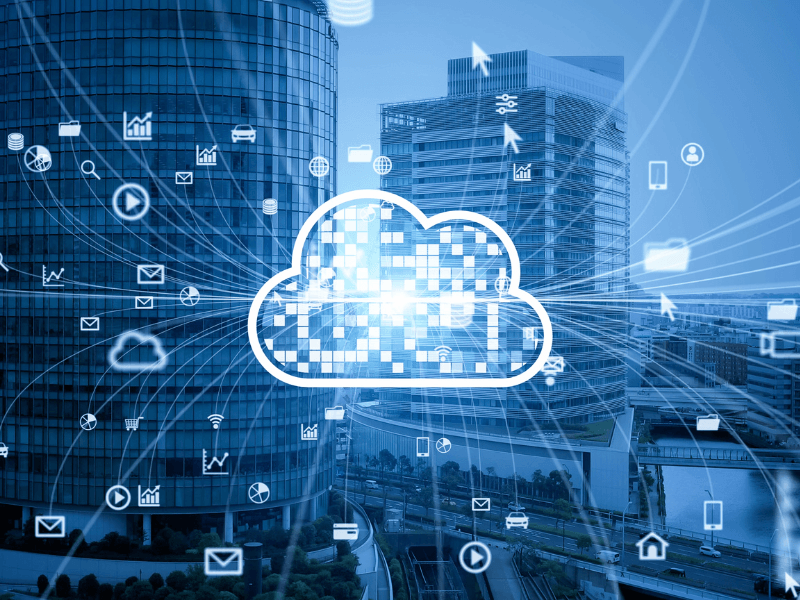
Why Choose Professional PCB Design Services?
In today’s high-stakes electronics landscape—from aerospace instruments and industrial automation to consumer IoT devices—a meticulously designed PCB ensures reliability, performance, and manufacturability. Attempting PCB layout without domain expertise can lead to costly failures: electrical noise, thermal hotspots, layout errors, or repeated manufacturing iterations. A robust PCB design service offers:
- Technical precision: Handling complex layouts—high‑speed differential pairs, RF, mixed‑signal integration—with signal integrity and EMI control.
- Manufacturing confidence: Deliverables optimized for real‑world fab and assembly capabilities, informed by DFM (Design for Manufacturability).
- Seamless handoff: Outputting complete packages—Gerber/ODB++, drill files, BOMs, pick‑and‑place data—ready for shop floor use.
- Iterative support: From prototype debug to post-production tweaks, ensuring designs perform as intended under real-world conditions.
2. Wagner’s End‑to‑End PCB Design Workflow
Wagner Engineering USA offers a comprehensive PCB design service with a clear, customer‑centric process:
• Project Definition & Requirements Gathering
They start with a technical consultation to understand project scope—from circuit function and form factor to environmental and regulatory constraints. Whether you provide a full schematic or just a concept, Wagner’s engineers clarify interfaces, component selections, and performance goals.
• Schematic Capture & Library Creation
Using top-tier EDA tools, Wagner translates circuit logic into detailed schematics. Every symbol, footprint, and 3D model is accurately vetted to prevent mismatches that often derail assembly.
• Board Layout & Component Placement
Placement is strategic: minimizing trace lengths for critical nets, optimizing thermal dissipation, and ensuring manufacturability. Multi‑layer designs benefit from layered stacking strategies that enhance EMI control and power delivery.
• Routing & Signal Integrity
Advanced layouts—including differential pairs, impedance-controlled traces, and RF paths—are meticulously routed. Wagner integrates signal‑integrity simulations to suppress crosstalk, reflections, and noise, ensuring the board behaves as intended.
• DFM, DFA & Compliance Checking
Before finalizing, they perform design rule checks, DFM and DFA analysis, thermal and EMC simulations to preempt fabrication errors and assembly issues. This reduces the risk of re-spins and production delays.
• Production Deliverables
Wagner delivers a full suite of documentation: manufacturing files, BOM, assembly drawings, pick‑and‑place files, and testing setup instructions. This documentation accelerates fabrication, assembly, and QC at board houses.
• Prototype Testing & Refinement
Recognizing that design validation uncovers real-world nuances, Wagner provides post-assembly debugging and refinement support—correcting any unforeseen issues and ensuring first-run success.
3. Domains of Expertise
Wagner’s engineers are well‑versed across industries:
- High-speed & RF systems: DDR, PCIe, USB, Ethernet, wireless modules.
- Dense or HDI boards: BGA, fine-pitch devices, stacked microvias.
- Mixed-technology boards: Rigid, flex‑rigid, and hybrid circuits.
- Industrial & automotive electronics: With an eye on thermal, EMC, and ruggedization.
Their adaptability—handling both simple single-layer breakout boards and 20+ layer HDI designs—sets them apart.
4. State-of-the-Art Tools & Technologies
To meet modern engineering demands, Wagner employs leading EDA platforms:
- Altium Designer – Multi‑layer design, 3D integration, collaboration tools
- Cadence OrCAD/Allegro – Ideal for high‑speed and constraint-driven workflows
- Mentor PADS, Xpedition – Common in defense/aerospace environments
Plus, signal‑integrity software like Simbeor ensures electrical performance meets expectations through virtual prototyping.
5. The Wagner Advantage
From user discussions and independent feedback:
- Wagner Engineering is based in the U.S. (Chicago area), enabling close engineer-to-engineer collaboration .
- They offer turnkey services—ranging from board layout to firmware, testing support, even prototype fabrication—depending on your needs .
- They emphasize accountability: staying involved beyond PCB handoff to support debugging and final tweaks.
- U.S.‑based presence facilitates NDA agreements, IP security, and responsive communication—advantages over offshore-only providers.
6. Simplifying Your Path to Custom Electronics
Step-by-step collaboration:
- Kickoff & NDA: Define scope, share schematics or concepts under an agreement.
- Preliminary design: Schematic capture and component library prep.
- Interactive layout review: Placement and routing drafts shared with you.
- Validation phase: Signal integrity, thermal, EMC, and manufacturability checks.
- Board release: Complete fabrication and assembly package delivered.
- Prototyping & debugging: Assembly coordination, functional testing, issue resolution.
- Production support: Final refinements, documentation handover, and vendor coordination.
7. Why PCBs Fail & How Wagner Prevents It
- Uncontrolled impedance: Causes signal distortion in high‑speed traces.
- Mechanical/Electrical mismatches: Incomplete libraries lead to assembly failure.
- Thermal bottlenecks: Heat buildup can reduce lifespan or compromise reliability.
- Manufacturing oversights: Hidden DFM issues cause fabrication delays or scrapped boards.
With deep technical review and cross-functional testing baked into their process, Wagner catches these problems before sending to production—saving time, cost, and headaches.
8. Cost, ROI & Timelines
Professional PCB design service like Wagner’s generally operate under:
- Project-based or hourly pricing, adjusted to board complexity (layers, high-speed, HDI).
- Prototype-to-production bundles, which may include assembly quotes and vendor selection.
- Faster time to market, minimal re-spins, and reduced downstream costs—accelerating ROI.
Though costs are higher than DIY PCB layout, savings downstream often outweigh that initial investment.
9. How to Engage Wagner
To engage:
- Prepare a one-page brief: concept, schematic/BOM (if available), desired board size, layers, key signals, environmental demands.
- Be clear on deliverables: schematic, Gerbers, BOM, simulation reports, etc.
- Clarify post-layout needs: debugging, testing, firmware integration.
- Address IP: establish NDA and clearly define ownership of deliverables.
- Set milestones: preliminary layout reviews, DFM sign-offs, prototype delivery.
10. Final Thoughts
PCBs are the foundation of reliable, performant, and safe electronics systems. Design excellence matters. With Wagner Engineering USA you get:
- U.S.-based collaboration, engineering rigor, and confidentiality
- Full-spectrum service from schematic capture to production-ready documentation
- Advanced technical expertise, insulated integrity, and rapid turnaround
- Delivery commitment, including hands-on debugging and iterative tuning
If you’re serious about delivering a high-quality electronics product—whether industrial control, consumer gadget, or aerospace-critical system—investing in turnkey PCB design services is not just smart—it’s essential.
Hiring a professional PCB design service like Wagner ensures your board is:
- Fully optimized for manufacturability
- Designed with careful electrical and thermal engineering
- Delivered with complete documentation for production
- Supported through prototype testing and final release
Eliminate uncertainty, accelerate delivery, and bring your electronics innovation to life—on time and on budget.