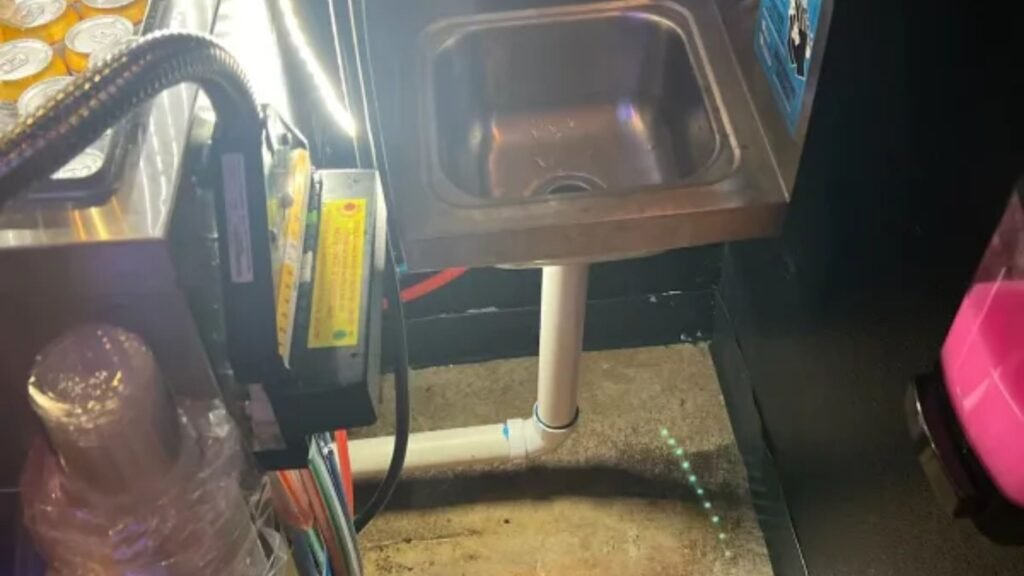
Every commercial kitchen, clinic, or shop with heavy foot traffic relies on one thing—working sinks. Not just for convenience. Clean hands, proper drainage, and leak-free plumbing are tied to health, safety, and smooth day-to-day operations.
When a technician walks into a business to inspect a sink, they aren’t just glancing at the faucet. They go layer by layer, chasing signs most folks don’t even see. That’s what makes commercial sink repair services so vital. Problems can sneak in silently. And when they do, repairs can get pricey fast.
Let’s dig into what a professional actually does during an inspection. It’s more than a five-minute look under the basin.
Starting at the Surface: Signs in Plain Sight
Technicians begin with the basics. The visual scan helps them spot obvious wear. But it’s not about cosmetics. It’s about damage hiding in plain view.
- Cracked caulking or loose seals? That can let water leak through and rot cabinets.
- Rust spots or bubbling metal around the drain? A clue that water’s been sitting too long.
- Scratches or warping? Not just a sign of use, but a hint at poor fit or older material.
They take notes on what they see. Even mild discoloration matters. That can show water backing up, or even improper cleaning chemicals that eat at metal over time.
Drain Flow and Backup Checks
Once the surface looks clear, the next step goes deeper. Techs run the water. Simple enough, right? But they’re not just making sure it runs.
They time the drain. If it takes more than a few seconds to clear, there may be build-up in the pipe.
They also check for gurgling. Strange sounds mean air is trapped, or something’s blocking the vent system.
And finally, they inspect the trap. That’s the U-shaped pipe just under the sink. If there’s a smell, a leak, or water pooled in the wrong spot, it often starts there.
Even sinks with perfect water flow can hide slow-forming clogs. Grease, food particles, and soap buildup don’t show up right away. But a seasoned tech hears and sees the signs.
Faucet Function and Pressure Control
Not all faucet issues show on the outside. Technicians twist each handle to full, and watch the spray pattern.
- If water splashes unevenly, they look closer at the aerator.
- If the pressure dips mid-flow, the valve may be old, or the supply line could be clogged.
- If the temperature jumps around or won’t change, the cartridge or mixing valve may be faulty.
They might remove the aerator and check for mineral deposits. In older buildings or with hard water, this happens fast.
Weak pressure? That’s a bigger sign. Could be a worn-out pipe or a shut-off valve issue farther down the line.
Seals, Gaskets, and Under-Sink Hardware
Many leaks hide behind the cabinet doors. So the next phase means crawling under the sink.
The tech feels along the pipes, valves, and joints. A small drip here can mean a soaked floor in a week.
- Are the gaskets dry and brittle?
- Are the compression fittings loose?
- Does the shut-off valve turn smoothly?
They might dry everything off first, then test again to spot fresh leaks.
They also inspect mounting brackets. Sinks that shift or creak when leaned on could be loose, putting strain on pipes. That small detail gets missed often but can cause full disconnects later.
Grime, Mold, and Smell Clues
It’s not all about metal and water. Smells matter too.
Technicians use their nose for more than just catching gas leaks. A musty odor under the sink can mean mold is starting to grow.
Discoloration on drywall or wood? That can point to old leaks. Even if everything is dry today, they log it for follow-up.
In commercial kitchens, techs often spot old food residue or cleaning chemical spills behind sink basins. These gather over time and can start corroding pipes or feed mold.
Sink Alignment and Mounting Stability
The structure holding the sink matters just as much as what runs through it. Techs check for wobble. Sinks that shake during use can stress joints and pipes.
If the basin doesn’t sit flat, it can lead to standing water. That’s where rust and bacteria thrive.
Wall-mounted sinks, common in some commercial bathrooms, get special attention. Loose bolts or shifted brackets are flagged for tightening or full reinstallation.
This is especially true for locations that saw older sinks installation in North Myrtle Beach and nearby coastal areas. Humid conditions there wear down fixtures faster.
Hidden Signs from Plumbing History
A good technician doesn’t just look at the sink. They look at the whole system. They ask about past repairs. They peek at neighboring fixtures.
If the sink is newer but the pipes are decades old, the mismatch often causes issues. Some shops cut corners with retrofits. Others skip regular maintenance.
They might find patches that aren’t up to code. Or traps installed backward. Or joints made from mixed metals, which corrode each other over time.
These silent mistakes show up later—usually with leaks, bursts, or odd smells. Early detection during an inspection prevents all that.
Behind the Walls: Listening for Bigger Problems
A final step some techs take is to listen. Not just with ears. With tools. Acoustic sensors can pick up vibrations from slow leaks inside walls. Moisture meters can show damp drywall even if there’s no stain yet.
That kind of inspection isn’t always needed. But in older buildings or those with complaints of water damage nearby, it can catch damage long before it grows.
No sink lives alone. It’s part of a bigger plumbing picture.
Conclusion: Why Regular Sink Checks Matter
Plenty of people think they’ll spot a problem when it shows up. But most sink issues brew quietly. One tiny leak, one loose joint, or one bit of gunk in the drain can set off a chain of problems.
That’s why regular sink inspections are so useful. A trained technician sees beyond the obvious. They spot wear, test pressure, check flow, and listen for the signs behind the walls.
For anyone seeking reliable, thorough, and honest work, Mia’s Master Plumbing stands out. Their technicians carry years of hands-on experience. They follow a full process during every inspection—nothing skipped, no guesswork. Each job gets real attention, from the visible surface to the lines hidden in the wall. Businesses across the area trust their team to spot problems early and solve them fast.
Their goal isn’t just fixing what’s broken. It’s making sure clients don’t face the same issue again. That focus on doing it right the first time has helped them earn trust from restaurants, clinics, shops, and more.